Optimizing Performance for Quattro Robot Control with EX Controller: Limitations and Recommendations
1.1 Purpose
To explain the factors that limit the EX Controller's ability to manage three or four Quattro Robots simultaneously.
1.2 Setup
Typical Vision Based Conveyor Tracking with PackManager (previously PackXpert) application and PLC Communication.
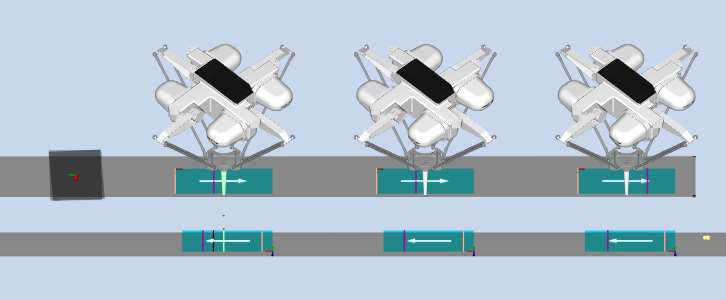
Figure 1
Software
ACE Versions 3.X and 4.X
V+ Versions 2.4 Edit C10
Hardware
Quattro 650/800 Robots
EX Controllers
2.1 EX Controller Specification
On Controlling 3 to 4 Robots
EX Controller controlling up to 4 Robots or 24 Axes is valid but is limited to a relatively slower throughput application, no belt tracking, and strictly V+ and ACE Sight programming. This is the hard limit that the software can support.
On CPU Usage
Quattro robot kinematics are more computationally intensive than the rest of the robots in Omron robot line-up. In addition to this, there are common items that consume processing power that need to be balanced:
1. Robot motion or trajectory computation on EX Controller (servo loop closed in eAIB)
2. PackManager (previously PackXpert) activity/overhead (monitoring activity in V+, monitoring of vision requests, monitoring of belt travel and latches received, updating of queues/buffers, commanding motion, etc.)
3. PLC Communication (amount of data being shared and efficiency of V+ Programs being used to communicate)
Conclusion
If the system involves PackManager (previously PackXpert) application, conveyor tracking, and PLC communication, it is generally conservative enough to limit the system to a maximum of 2 Quattro Robots per EX Controller that even with some inefficient V+ programming, the system will still have plenty of processing power to meet the system requirements.